Article de Yoann Lechat (EnvIM 2019)
I went to a roundtable in Beijing earlier this winter on Industry 4.0 and the benefits it can bring. The whole event was interesting and enlightening with renowned speakers, but not a word was expressed on sustainability issues. The question/answer part then came up and, taking the last question, I asked whether in the usage they are making of Industry 4.0, sustainability and ecology were one of the drivers. The silence following this question was, in itself, an answer.
Sustainability is a growing concern and the link to how the things we consume are produced is starting to emerge. The manufacturing industry which accounts, on a worldwide level, for 20% of the C02 emissions (IEA, 2014) has a big step to take to meet the various goals of carbon neutrality in 2050 and respect the engagement made in 2015 in Paris. Under the Paris Agreement, the parties agreed to keep global warming way under 2°C and try to keep it under 1.5°(Paris Agreement, 2015). In this matter, technology, and a new industrial revolution, can be seen as the perfect solution.
4th Industrial revolution
Currently, the manufacturing industry is going through a major change, which can be seen as the 4th industrial revolution (Caylar et al., 2016). The 1st one brought mechanization and steam power, the 2nd one mass production and assembly lines while the 3rd one transformed production processes through automation and electronics. The 4th revolution is making the digital and the physical world communicate and react in real-time. This is usually described as Industry 4.0
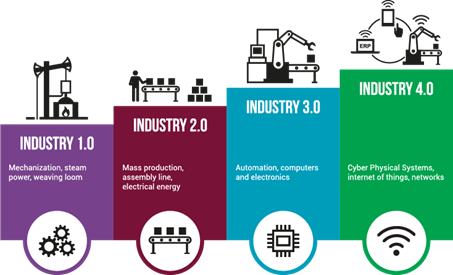
Industry 4.0
Industry 4.0 is an expression crafted in Germany in 2011 (BMBF-Internetredaktion, 2016) to preserve the country advance in manufacturing. The term encapsulates the aim to connect the virtual world and the material world, and blur the frontier between manufacturing and service. To realize this connection, a cyber-physical system is used by linking hardware and software to monitor data through sensors and activate actuators based on these data. This is made possible by the interconnection of all the different sensors and software through a network, creating the internet of things (Tim Stock et al., 2018). This allows the plant to react automatically to events that required human intervention previously, and so to act faster in a more optimized way.
Industry 4.0 is pushed by all the industrialized countries, sometimes under the equivalent term Industry of the future or Factories of the future. It can be seen in Germany through Industry 4.0, the US with programs Advanced Manufacturing or Manufacturing renaissance, in China with Intelligent Manufacturing or in Japan in Innovation 2. In the EU it is part of the program Horizon 2020 and Factories of the future while in France all these reflections are synthesized through the program Industry of the Future. (Rojko, 2017)
In the European program and the French one, this revolution is taking place within the moto of sustainable development which is based on three pillars: economic, societal, and environmental. It is explicitly mentioned in the documents provided for these programs, though no hierarchy between them is highlighted. This shows however the importance ecology took on the political stage and can be linked to the environmental events happening at the same time; the French plan came out the same year as the Paris COP21 giving birth to the Paris agreement.
Nevertheless, the papers published on the matter, in their vast majority, are focusing on the technical questions surrounding Industry 4.0 and the economic impacts and opportunities. The societal and environmental impacts are only rarely scrutinized. (Kamble et al., 2018).
When studied, the global expected impact is seen as beneficial thanks to an optimized use of material, water, and energy as well as new organizational and business models that can reduce waste. At the same time, the increasing amount of raw material and primary energy consumed is pinpoint as the environmental negative impacts (Tim Stock et al., 2018). The overconsumption of raw materials is a major and rising concern, especially for some critical ones such as gallium, tantalum, rare earth, which are on the EU critical raw material list (“Critical Raw Materials – EUR-Lex – 52017DC0490 – EN,” 2017). The extraction of these materials is consuming more and more energy and is increasing the environmental impact as it becomes strenuous to access them (Pilgrim, 2017).
One of the leading ways to reduce the demand for virgin material is the circular economy with recycling as one of its pillars. Yet, with the miniaturization and complexification of the alloy employed, the recovery of used material in the sensors and other devices utilized to implement industry 4.0 is difficult and energy demanding, when not impossible (Berthoud, 2017). For example, gallium and tantalum have a recovery rate of less than 1% while if copper has a recovery rate above 50%, the demand could be multiplied by 44 in 2035 from the 2012 use rate (Pilgrim, 2017).
On primary energy use, Industry 4.0 will increase consumption, mainly electricity, due to the increase in information and communication technology use. The sensors and RFID chips are predicted to be self-sufficient through micro-energy harvesting, while the constant connection of the products to data centers will create an increase in electricity consumption (Tim Stock et al., 2018). The automation part of Industry 4.0 will enable companies to run in not standard hours and so match with the peak production time from renewable energy and make full benefits of times when there is an oversupply on the energy grid. The development of renewable energy will so be able to grow, with one of the main weaknesses being overcome. Industry 4.0 brings interconnectivity and flexibility, and might be part of the development of industrial symbiosis through an easier optimization of flux, for example, companies will be able to sell excess process heat to plants in the vicinity or even to private consumers (Grischa Beier et al., 2015). To make one such change possible, an important number of infrastructures will need to be built and symbiosis in industrial parks or cities will need to be sought.
This creation of symbiosis and global connectivity is a major driver of the environmental benefits brought by Industry 4.0. Unfortunately, the main drivers for companies to implement Industry 4.0 are not environmental concerns or sustainability but profitability, efficiency, and human resources. According to Horváth and Szabó, Industry 4.0 needs to be driven by the ecological transition and considering its environmental footprint. There is no doubt, this 4th revolution will happen and as in the rest of our society, the digital will grow and create new possibilities, new business models. Until now, the digital transition is promising a dematerialization which sounds beneficial for the environment as the issue with extracting matters, and disposing of it is one of the biggest issues. But the environmental footprint of this transition is, for now, the opposite of these initial affirmations as the dematerialization of some usage does not equate to the dematerialization of the processes which allow it. Industry 4.0 needs to be given an environmental path to make sure the development brought is fully sustainable and beneficial for the planet (Morgane Créach, 2017).
One of the major levers to link the industry transition and the environmental needs is better regulations. The creation of regulation can define the path and specific incentives push the maturation of the ecosystem, as tried by the French government through the GreenTech incubators (Morgane Créach, 2017). Affixing the Industry 4.0 to some of the United Nations Sustainable Development Goals, such as the 7th “Affordable and clean energy” and the 12th “Responsible consumption and production” can help draw and promote the strong governmental program for environmental protection through Industry 4.0. This is the pedagogy part to bring together the different actors and create a common path enabling the global industry to play on an even field. Strict regulation still needs to be set to create a fast shift in the deployment and usage of Industry 4.0.
Sustainable manufacturing
Focusing on the 12th brings the question of sustainable manufacturing. This concept appeared before Industry 4.0; while it aims at manufacturing good sustainably, its definition has not reached a consensus yet (Anastasiia Moldavska et al., 2017). How to create a common goal and exchange between scientists, organizations, and policymakers when the concept itself is not clear and the same for everyone?
One of the options is to use another UN document, the Brundtland Commission report and the definition of sustainable development but applying it to manufacturing is not easy. It is also possible to use the general sustainable scope with the three bottom-line economic, social, and the environment with a real issue of making the tradeoff between the three realms (What is Sustainable Manufacturing?, 2014). Measure, plan, and review is the standard to have a good strategy, and it is the protocol when doing, for example, carbon footprint report. As norms exist for carbon accounting, like the ISO 14064 norm or the GHG Protocol, it is possible to compare two companies. Efforts are also made to consider the GHG offsets a company can produce through its products or its investments, on a science base methodology like the Net Zero Initiative (César Dugast, 2020). Standards are needed to allow a comparison and an accurate monitoring; it will be the same for sustainable manufacturing.
Moreover, as 70/80% of the product costs are locked in the designing phase (Saravi et al., 2008) as well as the environmental impacts (QUEROL, 2013), there is a strong need to plan and not only react. The development of labels, as the Ecolabel in the EU or the environmental grade in France, based on life cycle assessments, a standardized and normalized tool, can bring the company towards a global view and specific actions. The life cycle assessment takes a specific product and measures its environmental impacts, GHG emissions but also water eutrophication, acidification, air, and water pollution, …, from the extraction of the materials to its end of life, giving a complete understanding of the product impacts. It allows the company to comprehend the main areas of the product life in which lie the main impacts, and so where are the most important levers.
The link between Industry 4.0 and sustainable manufacturing needs to be made and drive the implementation of Industry 4.0. Synergies ought to be found between the environmental programs and the industrial ones, which will support projects transforming the way the industry and products are made. The goals and rules need to be defined early on to not subsidies the same expenditures (Enabling synergies between European Structural and Investment Funds, Horizon 2020 and other research, innovation and competitiveness-related Union programmes, 2014). More than saving money on some projects, co-benefits can increase the potential success of policies by creating them cost-effective and coherent which will help built general public support. To be able to define policies this way, a co-governance approach is needed. From intra-government information sharing and policy building to countries collaboration, harmonized co-governance approach demands to spread, and it can be supported by the international and regional organizations (Synergizing action on the environment and climate: good practice in China and around the globe, 2019).
The UN SDGs and the Paris agreement NDCs are powerful tools to create this global synergy and push for action policymakers, companies, and civil society. While Industry 4.0 is already driven by the potential economic benefits, a global approach with the environment protection being a non-negotiable element can bring along the general public approbation. All the above is soft laws and regulations, with no consequences allowing all companies and countries to continue business as usual. The path chosen until now is embedded in weak sustainability, a turn towards strong sustainability is needed as time is running out.
Manufacturing and strong sustainability
Strong versus weak sustainability is a debate on the status of natural and manufactured capital and their substitutability. Natural and manufactured capital are essentially different as the manufactured one is reproducible whereas the destruction of the natural one can be irreversible. Moreover, the production of more manufactured goods does not compensate for the loss of natural capital. (Jérome Pelenc et al., 2015) Choosing to follow a strong sustainability agenda is demanding with the requests to protect natural capitals and follow scientific opinions to produce laws and regulations. Creating strong environmental regulations has often been met with pushbacks on economic costs.
Strong environmental regulations are an innovation enabler by stopping a status-co and making a whole sector search for new solutions. The risks and requirements for regulations to bare the expected benefits are not all in the hands of the regulatory body as innovation and development of new business models are in the hands of scientists and companies, even if, often, regulation can pave the way. A high cost, inflexible standards and increasingly stringent regulations along the time are needed bricks, but also room and capabilities for innovation need to exist. (David M. Hart, 2018) A common work between soft law, like the SDGs, and strong regulations are required for an effective transformation.
The work achieved with the SDGs and all the environmental programs, based mainly on voluntary involvement, was necessary to create a sense of common goal. Now the shift needs to be fast and to initiate it, environmental regulations need to be crafted and enforced. Industry 4.0 has the opportunity to be part of a real revolution, a societal one with new modes of manufacturing products which then may induce a change in consumption habits.
In this time, the environment is becoming a key driver of the population in western countries as starting to be seen in population consumption patterns. (Magi, 2020) The re-industrialization of the west is wanted and with a deployment with environmental constraints, two opposite sides could be reconciled. Industry 4.0 as it is designed, driven, and implemented is not the green revolution needed to tackle the challenges upon us. Entangling it to strong sustainable industry and climate actions will change its route and enable success. It could be a step towards a sustainable society, the three pillars not on equal grounds but with the environmental one as the cornerstone to allow the economic and social ones to flourish.
–
Sources
Anastasiia Moldavska, Torgeir Welo, 2017. The Concept of Sustainable Manufacturing and its Definitions: A content analysis based literature review. Journal of Cleaner Production.
Berthoud, F., 2017. Numérique et écologie. RESPONSABILITÉ & ENVIRONNEMENT.
BMBF-Internetredaktion, 2016. Industrie 4.0 – BMBF [WWW Document]. Bundesministerium für Bildung und Forschung – BMBF. URL https://www.bmbf.de/de/zukunftsprojekt-industrie-4-0-848.html (accessed 2.18.20).
Caylar, P.-L., Naik, K., Noterdaeme, O., 2016. Digital in industry: From buzzword to value creation | McKinsey [WWW Document]. URL https://www.mckinsey.com/business-functions/mckinsey-digital/our-insights/digital-in-industry-from-buzzword-to-value-creation (accessed 2.19.20).
César Dugast, 2020. Net Zero Initiative Un référentiel pour une neutralité carbone collective. Carbone 4.
Critical Raw Materials – EUR-Lex – 52017DC0490 – EN [WWW Document], 2017. URL https://eur-lex.europa.eu/legal-content/EN/TXT/?uri=CELEX:52017DC0490 (accessed 5.4.20).
David M. Hart, 2018. When Does Environmental Regulation Stimulate Technological Innovation? A Synopsis of the Expert Literature for Policy-Makers. The Information Technology and Innovation Foundation.
Enabling synergies between European Structural and Investment Funds, Horizon 2020 and other research, innovation and competitiveness-related Union programmes, 2014. . European Commission.
Grischa Beier, Silke Niehoff, Achim Maas, 2015. Nachhaltigkeitsaspekte von Industrie 4.0.
Horváth, D., Szabó, R.Zs., 2019. Driving forces and barriers of Industry 4.0: Do multinational and small and medium-sized companies have equal opportunities? Technological Forecasting and Social Change 146, 119–132. https://doi.org/10.1016/j.techfore.2019.05.021
IEA, 2014. CO2 emissions from manufacturing industries and construction (% of total fuel combustion) | Data [WWW Document]. URL https://data.worldbank.org/indicator/EN.CO2.MANF.ZS (accessed 2.19.20).
Infodream, 2018. Industry 4.0 vs Industry of the Future? Infodream. URL https://infodreamgroup.com/industry-4-0-vs-industry-of-the-future/ (accessed 2.17.20).
Jérome Pelenc, Jérome Ballet, Tom Dedeurwaerdere, 2015. Weak versus Strong Sustainability.
Kamble, S.S., Gunasekaran, A., Gawankar, S.A., 2018. Sustainable Industry 4.0 framework: A systematic literature review identifying the current trends and future perspectives.
Magi, M.-S., 2020. Etude Havas 2020.
Morgane Créach, 2017. LE POINT DE VUE D’UNE ONG ENVIRONNEMENTALE.
Paris Agreement, 2015. . UNFCCC.
Pilgrim, H., 2017. The Dark Side of Digitalization: Will Industry 4.0 Create New Raw Materials Demands?
QUEROL, M., 2013. Sustainable Product Policy [WWW Document]. EU Science Hub – European Commission. URL https://ec.europa.eu/jrc/en/research-topic/sustainable-product-policy (accessed 5.8.20).
Rojko, A., 2017. Industry 4.0 Concept: Background and Overview.
Saravi, M., Newnes, L., Mileham, A.R., Goh, Y.M., 2008. Estimating Cost at the Conceptual Design Stage to Optimize Design in terms of Performance and Cost, in: Curran, R., Chou, S.-Y., Trappey, A. (Eds.), Collaborative Product and Service Life Cycle Management for a Sustainable World, Advanced Concurrent Engineering. Springer, London, pp. 123–130. https://doi.org/10.1007/978-1-84800-972-1_11
Synergizing action on the environment and climate: good practice in China and around the globe, 2019. . UNEP.
Tim Stock, Michael Obenaus, Sascha Kunz, Holger Kohl, 2018. Industry 4.0 as enabler for a sustainable development: A qualitative assessment of its ecological and social potential. Process Safety and Environmental Protection.
What is Sustainable Manufacturing?, 2014. . MIT.